Broad Prospects for Advanced Ceramic Manufacturing
Ceramic materials, known for their exceptional high-temperature resistance, corrosion resistance, and chemical stability, have been widely applied in various fields such as mechanical engineering, chemical industry, electronic communications, and biomedical applications. However, traditional ceramic processing methods are heavily dependent on molds and cannot meet the demands for rapid manufacturing of integrated, complex, and precision ceramic products. Compared with traditional ceramic processing technology 3D printed ceramics break the limitations. It can quickly produce fully personalized ceramic products without molds, has high structural design freedom.
The 3D-printed ceramic parts created by BMF are made from alumina, zirconia, and polymer-derived SiOC ceramics. These materials not only enrich market choices and enhance product performance indicators but also show a wide range of application prospects in high-end fields such as aerospace, biomedical, and electronic communications.
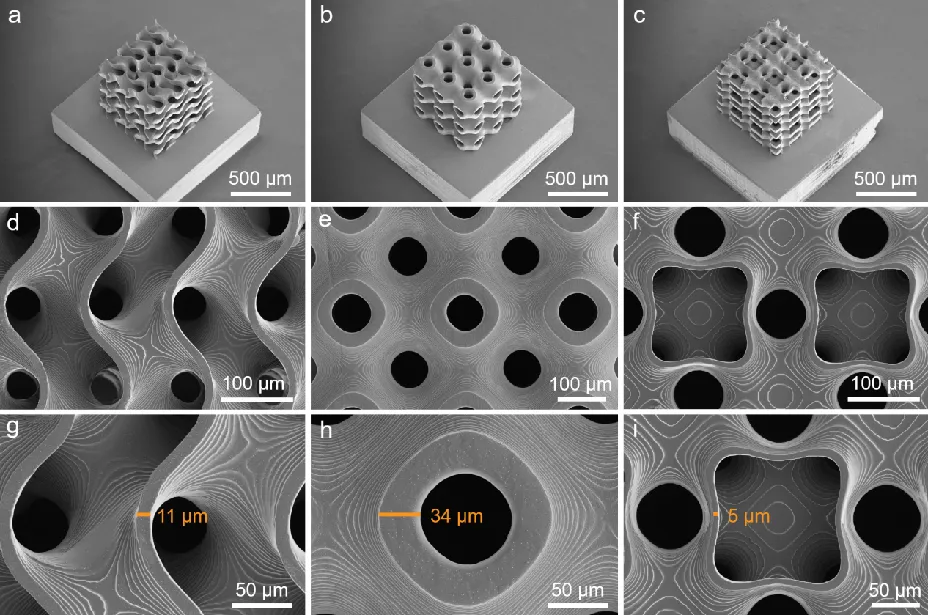
3D Ceramic Printing Empowers 5G Communication
The fifth generation (5G) technology requires highly integrated antennas, which drive base station filters to develop in the direction of miniaturization, lightness, complex structure, and low dielectric loss. The use of microwave dielectric ceramics to make 5G filters has become a key measure to achieve miniaturization and integration of base stations.
A research team from Central South University and Hebei University of Technology successfully prepared high-performance and high-precision Mg2TiO4 microwave ceramics using BMF’s microArch® S240 (resolution: 10 μm). They clarified the impact of processing parameters (laser power, exposure time, and layer thickness) on processing precision and dielectric performance, ultimately producing Mg2TiO4 microwave ceramics with a quality factor of 142,000 GHz.
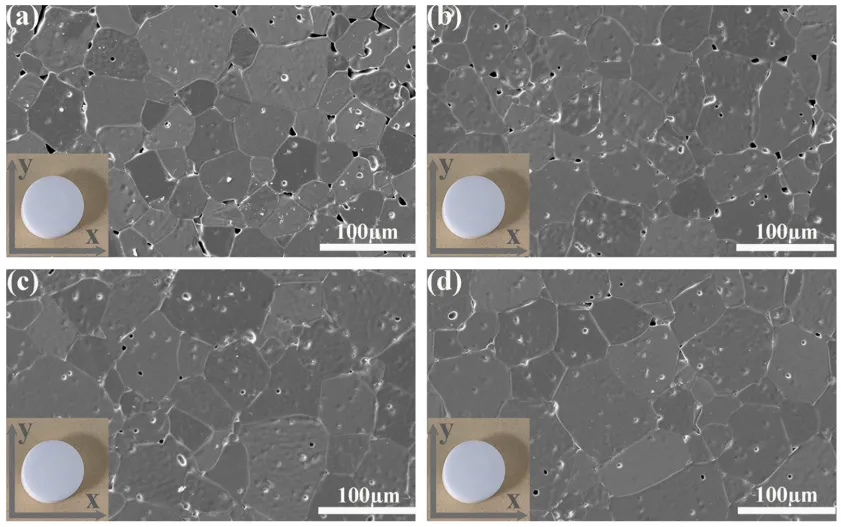
PμSL 3D printing technology can customize the printing of Mg2TiO4 ceramics with any structures and excellent dielectric properties, such as cylindrical and square column arrays, and filter substrate structures (with the minimum diameter of the cylinder is 440 μm and the layer thickness is 40 μm).
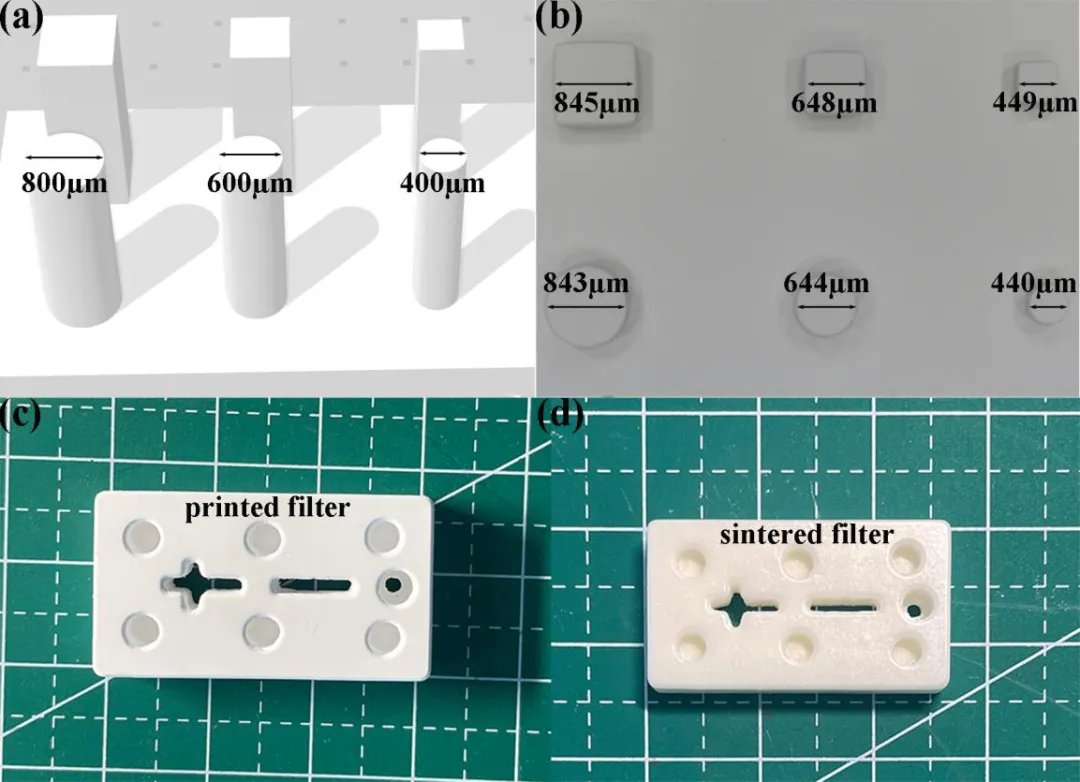
This preparation method successfully solved multiple problems of 3D printed functional ceramics, such as poor precision of formed samples, low density and lower dielectric properties than traditional forming methods. At the same time, this research provides a theoretical basis for the commercial application of 3D-printed ceramics.
This progress provides strong technical support for the manufacturing of miniaturized, high-performance filters, which is of great significance for meeting the demand for high-performance filters in the 5G/6G communication field.
Ceramic Additive Manufacturing Technology Achieves Bone Regeneration
A research team from Shanghai Jiao Tong University, using BMF’s microArch® S240 (resolution: 10 μm) high-precision 3D printing equipment, successfully prepared a bioactive glass scaffold.
The scaffold uses a special process to help graphene oxide (GO) to be stably and evenly fixed on its surface. The research team inoculated and cultured bone marrow stem cells, venous cells and cytokines on the scaffold. This experiment showed that the scaffold can effectively promote the formation of capillaries and bone tissue.
Based on its excellent performance, the scaffold is expected to be used in the treatment of bone defects in future clinical practice, providing patients with more effective treatment options.
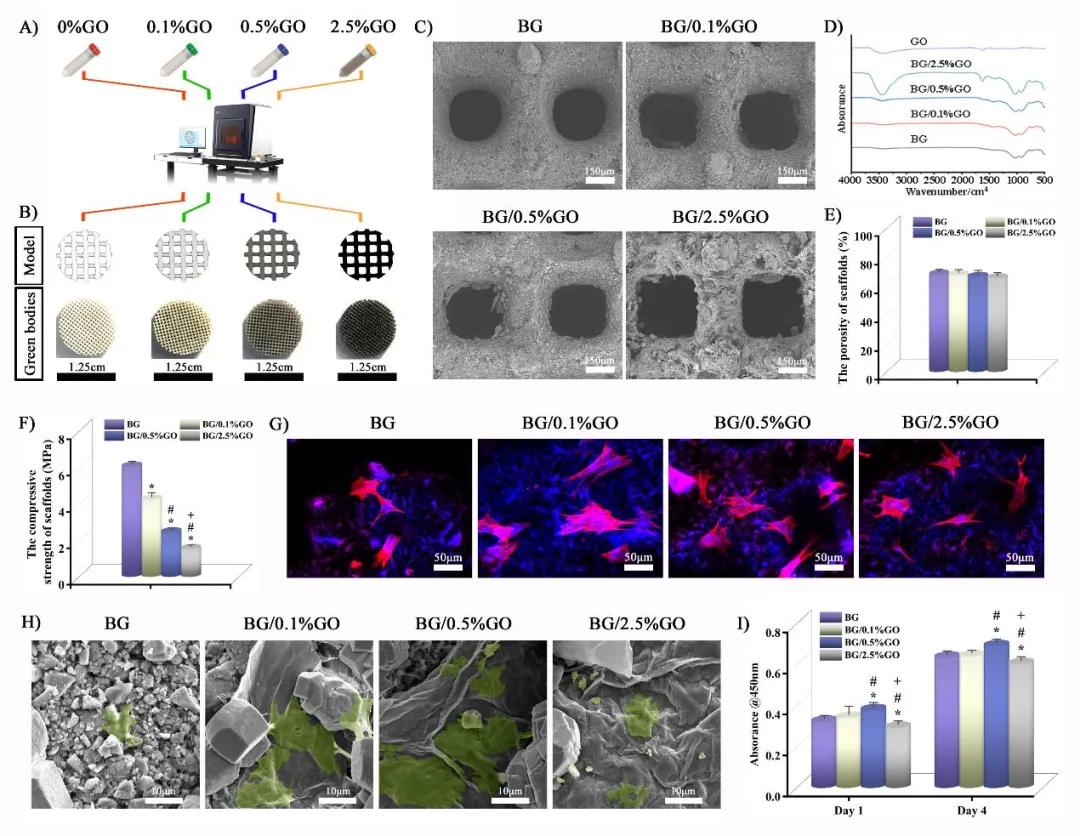
Milestone in Dental Restoration: Ceramic Printing Aids Non-Invasive Treatment
In addition, a breakthrough terminal application result in the field of dental restoration by BMF is the ultra-thin veneer, which is one-third the thickness of other competitors, preserving more of a patient’s enamel than traditional veneers and making the process of straightening and whitening teeth simple and painless for many customers.
This technological advancement marks a significant shift from traditional invasive therapy to non-invasive therapy in dental restoration technology, greatly enhancing the level of technical skills and service quality in dental restoration treatment.
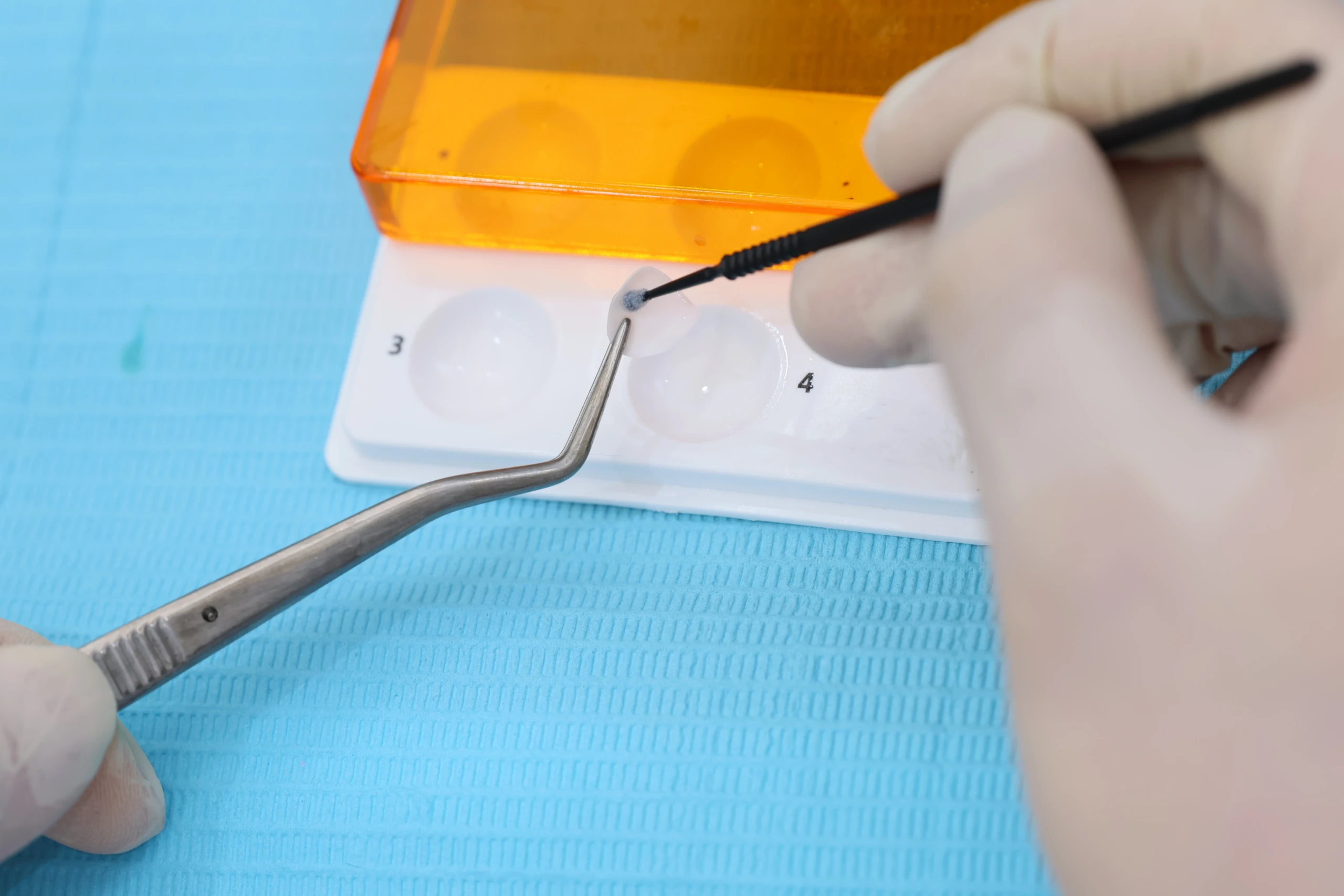
In the current field of advanced ceramic manufacturing, additive manufacturing technology has become one of the most promising key development directions, bringing revolutionary new opportunities to the production of ceramic components with its unique fine-forming capabilities. The technology not only improves the precision and complexity of products but also optimizes the efficiency of material use. Looking to the future, with the in-depth development of technology and the gradual reduction of costs, the application fields of ceramic additive manufacturing technology are expected to significantly expand, which will greatly promote the release of market potential and the expansion of industry scale.
BMF will continue to commit to expanding the boundaries of material science and technological innovation, bringing unprecedented design freedom and performance enhancement to fields such as mechanical engineering, communication engineering, aerospace, and biomedicine, to achieve more efficient, more precise, and more cost-effective ceramic component manufacturing.