The advent of the era of artificial intelligence has accelerated the development of the intelligent robot industry, and humanoid robots with tactile perception have also seen an increase in applications.
Tactile sensors are important devices for robots to directly perceive the effects of the environment, and can detect environmental contact force, temperature, humidity, hardness, material and other characteristics. The more sensor units per unit area in a tactile sensor device, the higher the resolution, and the more accurate the characteristic information obtained.
Micro 3D printing technology can be used to efficiently fabricate sensor devices with high resolution and high tolerance control capabilities, which is also the reason why many education and research institutions choose.
A team from the Hong Kong University of Science and Technology (Guangzhou) has developed a triboelectric bimodal intelligent tactile sensor (BITS). This sensor can identify the hardness, type of material, and quantify the modulus. This research provides a new idea for promoting the application of skin-like tactile sensors in multimodal signal detection as well as quantifying Young’s modulus of the materials. The research team used BMF’s Projection Micro Stereolithography (PμSL) 3D printing technology to miniaturize the BITS structure, successfully integrated into electronic skin. This innovation has provided a more realistic tactile perception capability for robots, prosthetics, and actuators, promoting the development of multimodal tactile sensors.
The achievement was published in the academic journal Science Advances under the title “Biomimetic Bimodal Haptic Perception Using Triboelectric Effect.” Click here to read the original article.
Highlights:
- BimodalTactile Perception
The BITS sensor can simultaneously identify the softness and type of materials, providing a greater amount of information than traditional tactile sensors.
- PμSL3D Printing Technology
Using BMF PμSL 3D printing technology, the research team has successfully miniaturized BITS, improving the accuracy and integration of sensors, and providing a new solution for the design of electronic skin.
- Stability and Reliability
Tests conducted under various conditions have demonstrated that the BITS sensor can maintain signal stability, confirming its reliability in practical applications.
Innovative Breakthrough in Tactile Sensors
Tactile sensors play a vital role in how humans gather information and receive feedback about their surroundings. The triboelectric bimodal tactile sensor (BITS) developed by the team has taken traditional tactile sensors to a new level, providing more realistic tactile perception capabilities for robots, prosthetics, and actuators.
Application of 3D printing technology
BMF’s PμSL 3D printing technology offers a unique and reliable solution to achieve the highest level of precision at the required sizes for education and research institutions. In this study, micro 3D printing technology played a crucial role. The research team used BMF’s Projection Micro Stereolithography (PμSL) 3D printing technology to miniaturize the BITS so it can be integrated into the electronic skin. The application of this technology not only enhanced the precision and integration of the sensor, but also provided a novel solution for electronic skin to obtain more multidimensional information.
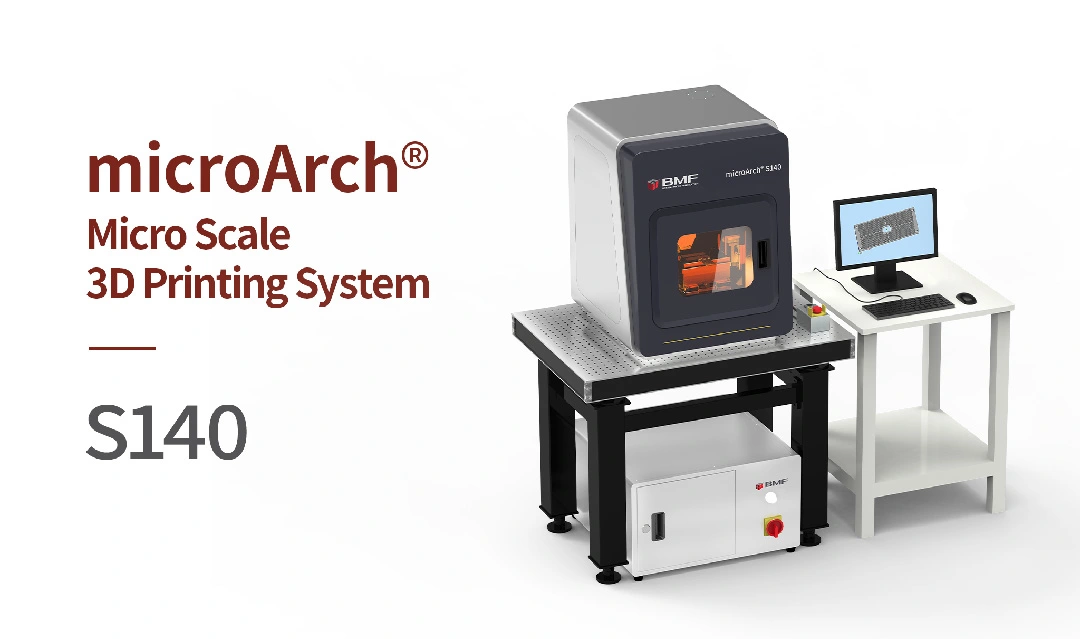
Equipment used in this research: S140 (resolution: 10 μm)
Distinctions and advantages of BITS
- Innovative Design:Inspired by the antennae of insects, the BITS sensor is designed with a hemispherical dome structure, capable of generating different voltage signals when in contact with objects of varying softness.
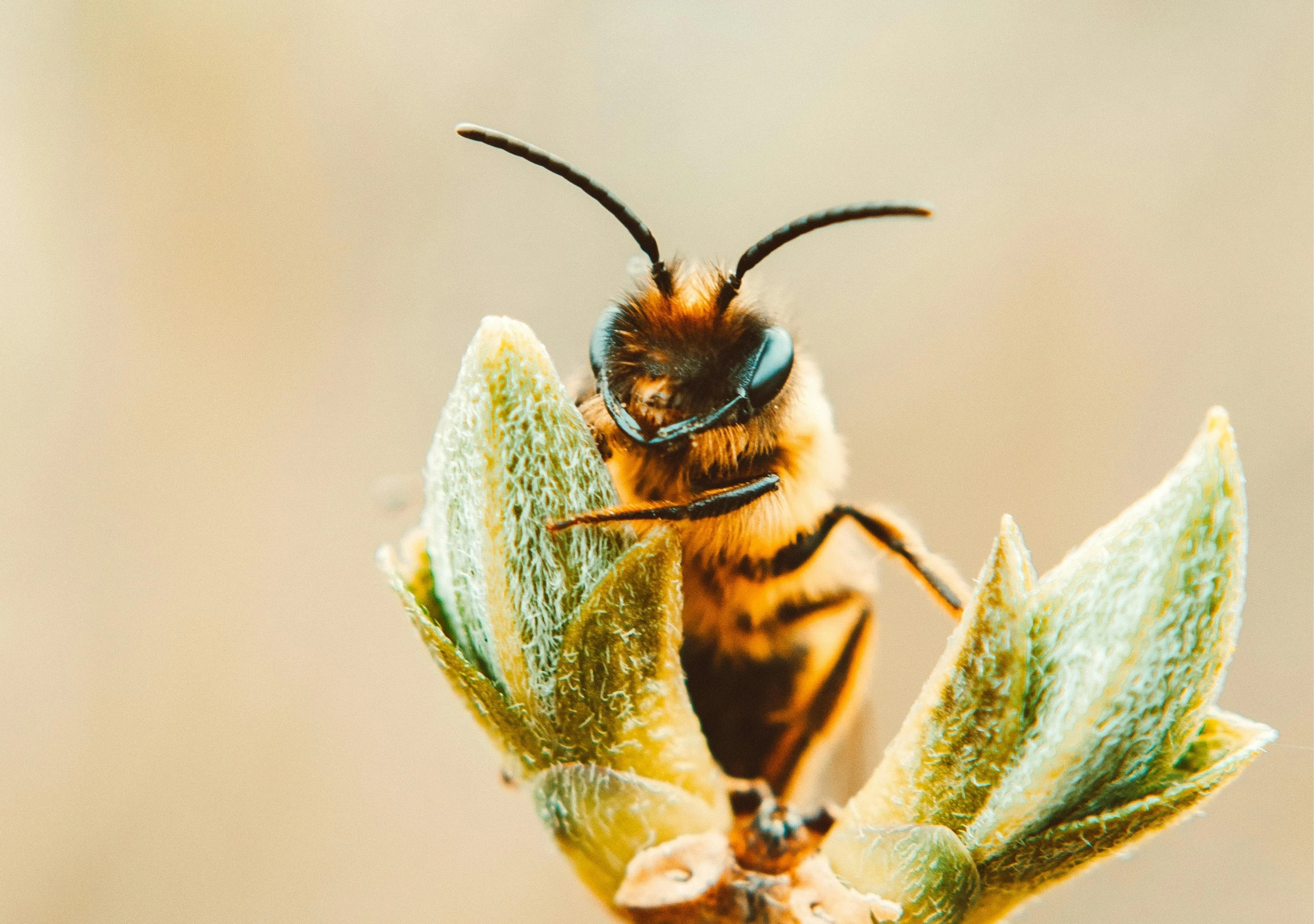
- BimodalTactile Perception:This sensor can identify the softness and type of materials simultaneously. It combines the triboelectric effect and the Hertz contact theory to identify the softness of materials by measuring contact height and pressure, and identifies the type of material through the voltage signals produced by different friction layers against different materials.
- High-PrecisionIdentification:Through machine learning algorithms, the BITS sensor can achieve high-precision identification of material types and softness.
- Stability Testing:Tests conducted under different conditions show that the relation between the BITS sensor’s voltageand contact height remains linear, and the signal is stable during long-term continuous testing.
- Miniaturization Potential:The research team also verified that sensors of different sizes all exhibit a good linear relation, showing the potential for sensor miniaturization.
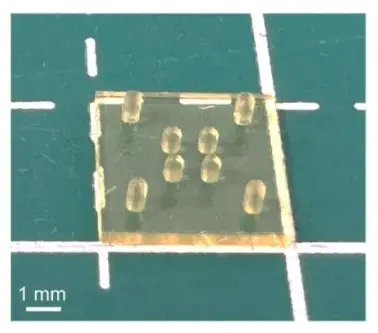
Printed by microArch® S140
- Application Prospects:This study provides a new solution for electronic skin to obtain moreaspects of information and is expected to be widely applied in the fields of robotic and prosthetic tactile perception systems.
3D printing technology, with its unique innovation and flexibility, has become an indispensable tool in the field of scientific research, and can also provide high-precision, customized, and small-batch manufacturing solutions for industries.
To learn more about how our solutions could help increase the quality of your parts production or future innovation, please contact us now.