Highlights:
- Modular ExtruderHead Design
A modular design is proposed to manufacture fibers with controllable periodic structures using 3D printing technology, which simplifies the complexity of traditional extruder heads, improves manufacturing efficiency, and easily adjusts the internal structure of fibers to achieve diverse functional requirements.
- Significant Enhancement in Mechanical Performance
The fiber structures used in the study have achieved a breakthrough in mechanical performance, especially in fracture toughness.
- Spatially Programmable 3D Structures
By precisely controlling the printing path, spatial programming of periodic structures in 3D wooden pile structures has been realized, allowing the 3D printed structures to show better performance in compression tests, which are 4.3 times and 6.5 times higher than traditional composite materials respectively.
3D printing technology has become one of the driving forces of innovation that cannot be underestimated.Among them,micro 3D printing technology has been applied in various cutting-edge fields,and continuously demonstrates its unlimited potential.
The research team from Westlake University recently developed a revolutionary modular extruder head design, using BMF’s high-precision DLP 3D printing equipment (resolution: 10 μm) and Direct Ink Writing (DIW) technology to achieve a multi-material direct writing process, producing programmable periodic filament structures. This innovation not only simplifies the manufacturing process but also greatly improves production efficiency and realizes the versatility of materials.
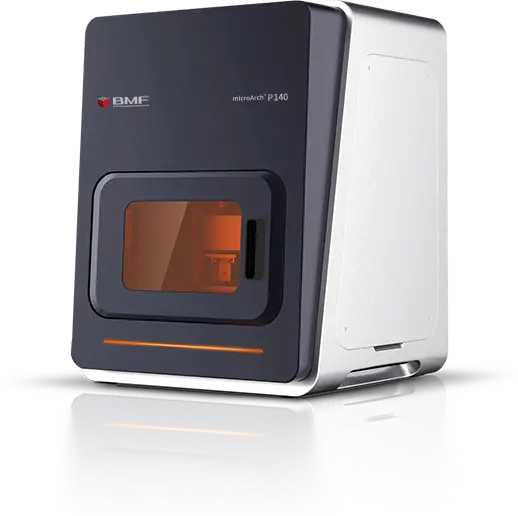
The result has been published in the academic journal Additive Manufacturing under the title “Multimaterial extrusion of programmable periodic filament structures via modularly designed extruder heads.”
Click for the full paper: https://doi.org/10.1016/j.addma.2024.104234
Significant Enhancement in Mechanical Performance
Through this modular design, the research team successfully manufactured fibers with significantly enhanced mechanical properties. For example, the layered structure of the soft/hard PDMS composite elastomer has a fracture toughness several times that of traditional materials. This not only demonstrates the great potential of PμSL 3D printing technology in enhancing material performance, but also provides more powerful material choices for industrial applications.
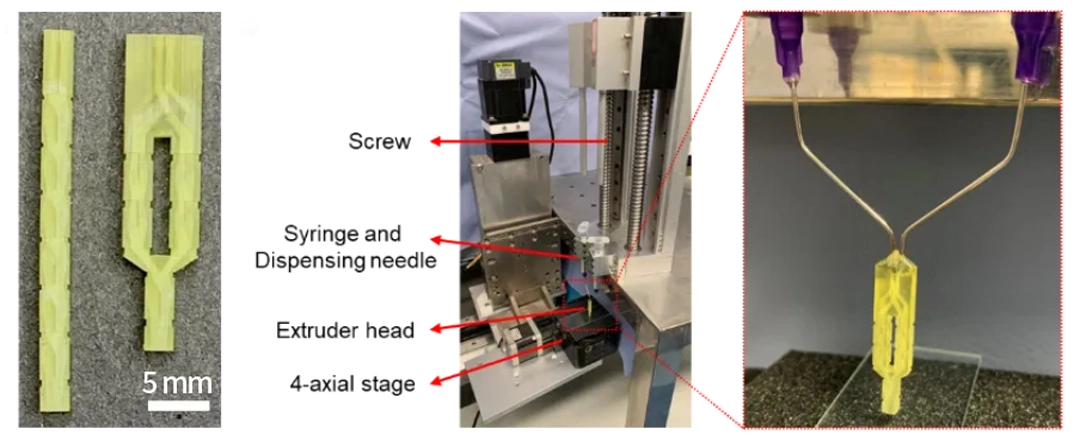
Spatially Programmable 3D Structures
What’s more astonishing is that BMF’s 3D printing technology can also achieve spatial programming, precisely programming periodic structures in 3D wooden pile structures by controlling printing paths. This capability enables 3D printed structures exhibit higher toughness and energy absorption capacity in compression tests, which are 4.3 times and 6.5 times higher than traditional composite materialsrespectively.
BMF’s micro 3D printing technology is not only a catalyst for various scientific research achievements, it also represents the future of industrial manufacturing. We sincerely invite you to join this technological revolution to explore more innovative possibilities together. Choose BMF, choose a future full of infinite potential.
BMF will continue to provide 3D printing technology and service consultation, if you have any needs, please feel free to contact us.