The development of glass materials dates back to B.C. The earliest glass products were found in ancient Egypt and Mesopotamia. As time went by, the glass manufacturing technology has been gradually developed and improved, evolving from the initial hand-blown to the later industrialized production. The applications of glass have also expanded from decorations and containers to architecture, scientific instruments, optical devices and other fields.
Silica glass, a special glass material made of high-purity silicon dioxide (SiO2) composition, has stable physical and chemical properties such as high-temperature resistance, chemical stability, low thermal expansion, transparency, and electrical insulation. Its strong material properties make it widely used in industrial and scientific research fields.
Despite many advantages, its inherent characteristics of high hardness and brittleness present difficulties in processing. At present, the preparation of traditional quartz glass microstructures faces many challenges such as complex processes, high costs, and fragile materials, and there are still huge difficulties in realizing three-dimensional structures.
Based on this, researchers from the Hong Kong Polytechnic University and the University of Hong Kong have proposed a method for creating three-dimensional silica glass structures with sub-micron features and larger millimeter/centimeter dimensions using BMF PμSL 3D printing technology. Their findings have been published in the journal Nature Communications under the title “One-photon Three-dimensional Printed Fused Silica Glass with Sub-micron Features.”
The researchers chose silica nanoparticles and two types of acrylates as polymer precursors, ensuring good compatibility and dispersion of the silica nanoparticles. Combined with PμSL 3D printing technology, high-performance transparent silica glass with complex three-dimensional microstructure can be flexibly constructed. The resolution, molding speed and printing formats surpass most other 3D glass printing technologies.
The silica glass samples in this study were produced by the BMF microArch® P130 (2 μm) ultra-high precision 3D printing system. The relevant technology has been patented and will be commercialized in cooperation with BMF.
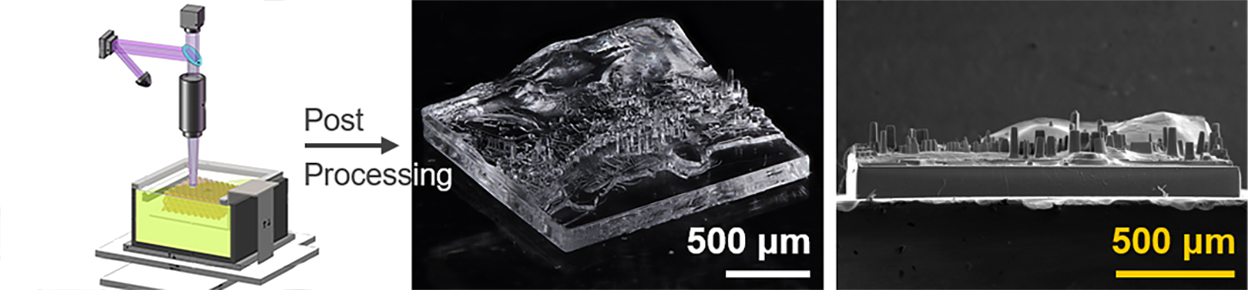
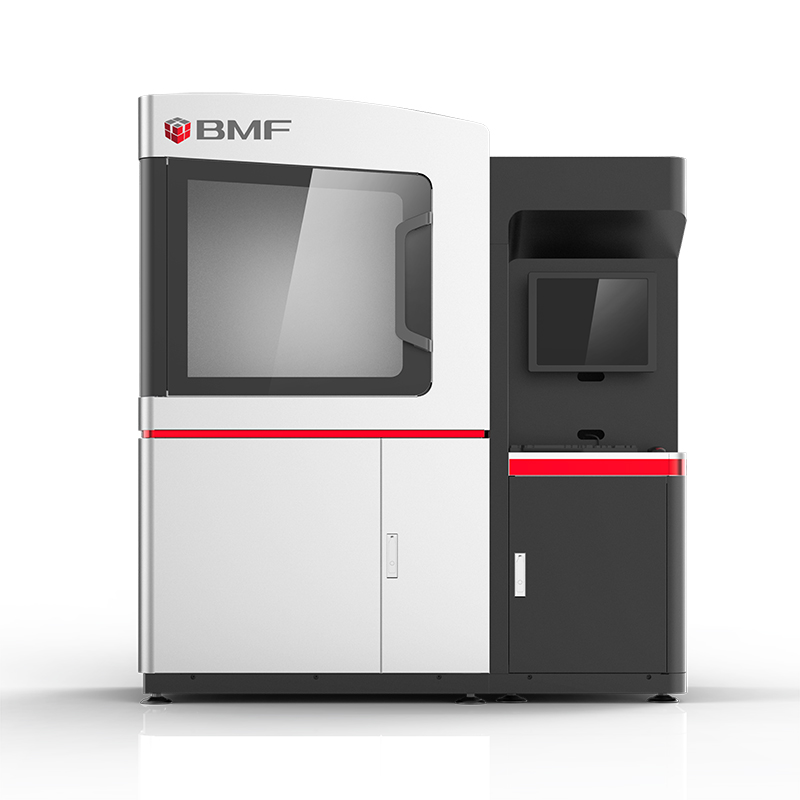
For more experimental data and details, please refer to the publication at the following DOI link:
https://doi.org/10.1038/s41467-024-46929-x
If you are interested in harnessing the power of micro-scale 3D printing technology to advance scientific fields, please reach out for more information.