There is a growing demand for wearable e-skin devices in the current market as it is extremely useful in monitoring various health signals, particularly in the biomedical industry, surgical robot industry, and brain-computer interface (BCI) industry. Moreover, with advancements and innovations in current technology, an increasing number of researchers are working on providing additional features to wearable e-skin devices.
In a recent study titled “An Asymmetric Interlocked Structure with Modulus Gradient for Ultrawide Piezocapacitive Pressure Sensing Applications” published in Advanced Functional Materials, researchers from Fudan University have developed a wearable e-skin sensor, based on an asymmetric interlocked structure with a modulus gradient for ultrawide piezocapacitive pressure sensing applications. Using BMF microArch® S130 (2μm), they built extremely intricate parts with excellent precision and tolerance in an interlocked structure.
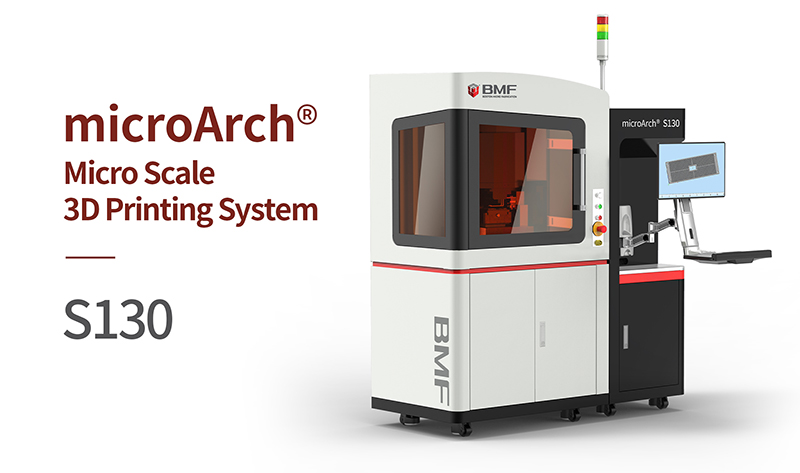
This wearable e-skin device has the potential to optimize the medical industry, offering real-time monitoring of health status and personalized treatments. However, some of the main challenges with these e-skin devices are their structure and fabrication. Therefore, 3D printing technology can pave the way for this.
microArch® S130, from BMF 2μm series of micro additive manufacturing solutions, is an ideal option for educational and research institutions with requirements for ultra-high resolution, accuracy, and precision. BMF micro AM technology can print high-precision and complex structural models, such as electronic sensors, e-skin sensors, and microfluidics, for wearable devices.
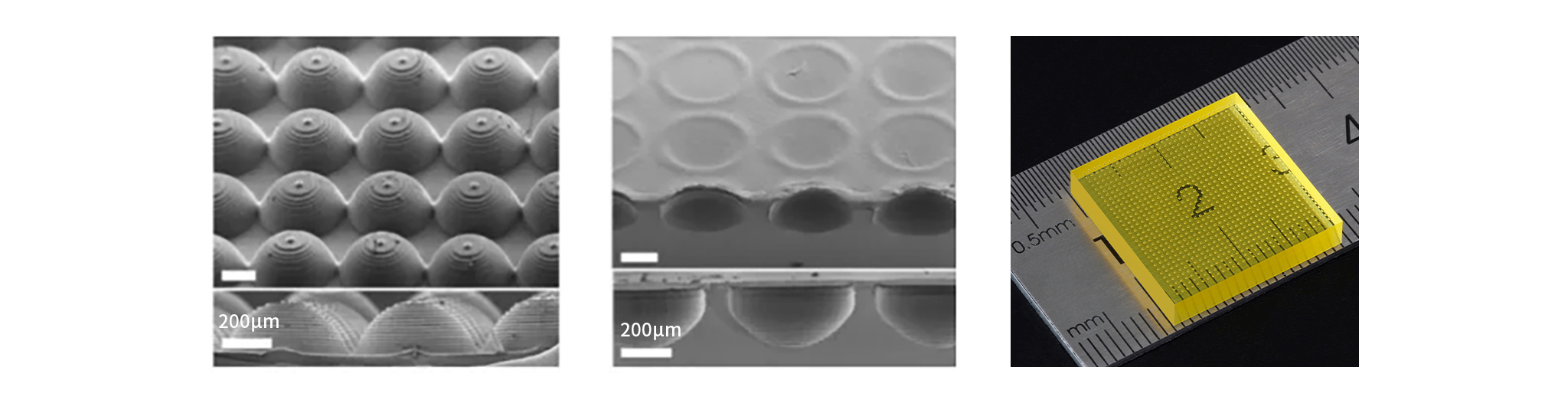
Constant and advanced research will be helpful in innovative products that are extremely inclusive, beneficial and efficient. The fitness and improvement in people’s lifestyles will also drive the demand for healthcare market during the forecast period.
To learn more about how micro 3D printing can benefit your applications, please contact BMF.
For additional information, you may read the complete research paper here