In the field of sensors, a breakthrough study is changing the way we interact with machines. A research team from the Southern University of Science and Technology, the University of Science and Technology of China, and the Commercial Aircraft Corporation of China Ltd has successfully developed an ultrafast piezocapacitive soft pressure sensor, leveraging micro-scale printing technology to achieve unprecedented sensor performance. The related results were published in the academic journal Nature Communications under the title “Ultrafast piezocapacitive soft pressure sensors with over 10 kHz bandwidth via bonded microstructured interfaces.”
This electronic skin can detect pressure changes from static to dynamic with extremely high sensitivity, and its response speed reaches an astonishing 12500 Hz. This achievement is attributed to the team’s use of integrated microstructured interface bonding technology and the percolation transition sensing mechanism of elastomer-carbon nanotubes. With the BMF microArch® S130 3D printing equipment, the research team was able to print microcone structure templates with a precision of 2μm, featuring a diameter of 50μm and a height of 40μm, which is crucial for enhancing the sensor’s performance.
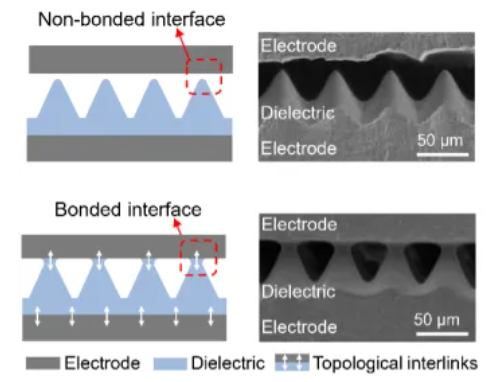
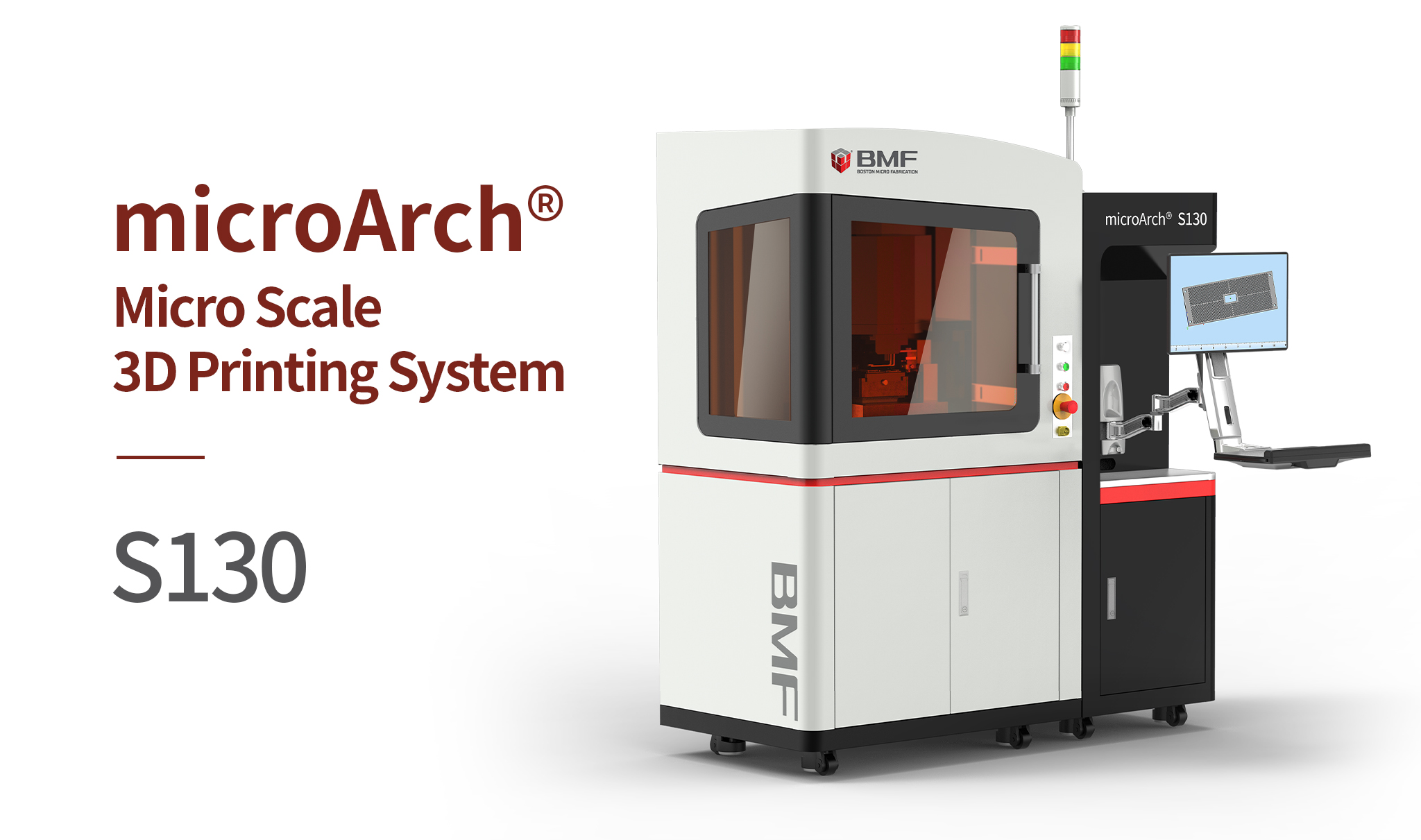
The key to this technology lies in the 3D-printed microcone structure, which not only reduces energy dissipation during dynamic loading and unloading, but also significantly improves the responses and recovery speed of the sensor. By adjusting the height, initial contact area, and cone diameter, the research team achieved a perfect balance of low energy dissipation, high sensitivity, and high mechanical stability.
Furthermore, the team also demonstrated the potential application of this sensor in the field of acoustics, by designing an artificial ear system for sound detection, demonstrating its sound recognition capabilities comparable to commercial microphones.
The success of this study highlights the significant role of micro 3D printing technology in the manufacturing of flexible electronic sensors and provides a new direction for the development of future smart devices. As technology continues to advance, we look forward to the emergence of more innovative applications that will make human-machine interaction more natural and efficient.
For more information:
https://www.nature.com/articles/s41467-024-47408-z
We also look forward to your opinions or suggestions and hope to explore new possibilities of the world from a microscopic perspective together with like-minded individuals.